Industrial Internet of Things (IIoT) technology has the potential to enhance user benefits through diagnostics, analysis, and predictive maintenance.
Imagine this scenario: An operator on a beer bottling production line suddenly encounters equipment downtime. The operator does not need to access the programmable logic controller program or interrupt the network. Instead, the operator simply takes out a smartphone, connects to the machine's pneumatic valve system, opens a web page, and views diagnostic data that displays the performance of the equipment's pneumatic system. It is found that the electromagnetic coil in the directional control valve is burnt out, and this directional control valve controls an actuator of the machine. Within minutes, maintenance technicians can connect a new control valve, and the bottling production line is operational again, with almost no production loss or major control system intervention.
This hypothetical example demonstrates one of the many advantages that new industrial Internet of Things (IIoT) technology can bring when entering the machine control market. These IIoT-supporting technologies are expected to improve user benefits through better diagnostics, analysis, and predictive maintenance. As a result, users can increase productivity, reduce downtime, and lower maintenance costs to achieve an unprecedented level of operation.
IIoT technology is still in its infancy, and its current implementation in the machine control environment is mostly experimental. In these experimental applications, manufacturers are identifying small, centralized production issues and then adopting IIoT solutions at the basic level to address these issues. Gateways export data from the machine's control system for analysis and storage on-site or in the cloud. Remote operation analysis can provide a better understanding of the issues and point out solutions.
Advertisement
For example, a production supervisor may be concerned about the machine's peak energy consumption. The energy utilization data of the equipment is correlated with other operational data extracted from smart sensors installed on the machine. By analyzing the correlated data, the production supervisor can identify when the peak power consumption occurs and the factors affecting operations.IO-Link provides connectivity at the device and sensor level, even allowing the smallest field devices and intelligent sensors to transmit their diagnostic data for analysis to understand functionality and system status. Image source: Emerson Automation Solutions.
The Backbone of Machine Control
As more IIoT-based devices and networks enter the market, today's pilot projects could become tomorrow's full-plant projects. New architectures combine intelligent devices (such as sensors, I/O modules, servo drives, robots, motor starters, etc.) with intelligent pneumatic valve systems, including integrated industrial network interfaces, I/O, and local analytical capabilities. These smarter interconnected devices will become the backbone of machine control and connect with the IIoT.
While industrial networks have been used in higher-level equipment for decades, integrating them into small field-level sensors was too expensive. Adding point-to-point communication technology (such as IO-Link communication) used in existing wiring infrastructure can extract data from intelligent sensors and devices. Wireless connections, mobile devices, and the combination of wireless diagnostics and predictions provide the analytical capabilities needed for IIoT applications for intelligent pneumatic manifolds. These technologies transmit data from field devices (intelligent sensors) through the pneumatic manifold to the machine control system.
These diagnostic and predictive data can also be routed through separate gateways and channels that do not belong to the control network. This allows external devices to effectively collect, analyze, and process relevant process data without loading diagnostic data into the control network. It also allows users to analyze this data without affecting the machine process or production plan. This IIoT-driven data analysis can also be achieved by retrofitting existing machines.New machine components and networking devices supporting IIoT (Industrial Internet of Things) technology are being introduced to the market. The new architecture combines intelligent devices with smart pneumatic valve systems, integrating industrial network interfaces, I/O, and local analytical functions.
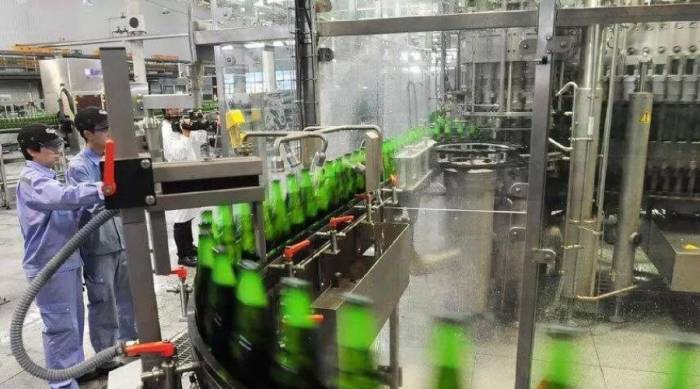
The Role of IO-Link
IO-Link (IEC 61131-9, a communication standard for sensors and actuators) allows the smallest field devices and intelligent sensors to transmit their diagnostic data for analysis, to understand system functionality and status. IO-Link technology is designed to set and change functional parameters on intelligent sensors using the same connection medium. It has evolved into a communication technology that can control non-sensor devices, such as proportional pressure regulators and valve systems.
IO-Link is typically used in conjunction with communication gateways, connecting to higher-level industrial networks such as EtherNet/IP, Profinet, and EtherCAT, to allow network communication to reach the lowest level of control systems. Through these IO-Link master gateways, intelligent devices can send diagnostic and predictive data digitally to advanced processors for analysis, which can be done locally, on-site, or in the cloud.
New Modular Fieldbus Valve Assemblies
The new modular fieldbus valve assemblies also have the advantage of hosting multiple IO-Link master stations, which can act as gateways for Ethernet communication nodes. This eliminates the need to establish a communication node for each IO-Link master station, thereby reducing costs and complexity.
Due to the modular nature of current fieldbus manifolds, the IO-Link master module designed for integration into modular fieldbus valve manifolds can also be distributed within a 30-meter range from the fieldbus communication node. This facilitates the convenient arrangement of sensors and devices on the machine. The IO-Link master station module can provide auxiliary power connectors for each independent IO-Link channel, offering machine designers greater flexibility, efficiency, and additional safety options.Integrate local Wi-Fi communication into the pneumatic valve system to simplify machine maintenance and commissioning. Users can easily access data through any mobile device that supports Wi-Fi without the need to download any applications. Operators or maintenance technicians connect their mobile devices to the Wi-Fi network and provide the device with an HTML web page featuring machine analysis data in an appropriate format.
Implementing IIoT Across the Entire Plant
After completing local experiments, it will be easier to implement IIoT technology across the entire plant, generating substantial benefits in terms of machine uptime, operator safety, commissioning, and product quality.
Through predictive maintenance, IIoT technology can reduce machine downtime, enabling operators to identify and resolve issues in a planned and orderly manner without interrupting the production process. Prediction allows for real-time analysis, enabling continuous monitoring of machine performance without increasing the overhead of the control system. The timing, distance, and service life of directional control valves can be monitored. When deviations from normal operating parameters occur, warnings are issued to the user. Prediction is an important step beyond preventive maintenance, helping to adjust, repair, or replace parts before they affect machine performance.
IO-Link communication technology allows low-level devices to communicate with advanced networks in a simple but cost-effective manner. This also brings industrial communication to the smallest devices, fulfilling the promise of IIoT.Wireless connectivity also allows maintenance personnel to monitor the pneumatic valve system and the equipment connected to it in hard-to-reach positions inside the machine. They can diagnose broken wires, non-operational communication modules, or faulty valve coils without shutting down the system or climbing on the equipment.
Maintenance personnel can also use mobile devices to check the status of IO-Link sensors at any time. New smart sensors will alert users to whether they are damaged and the cause of the failure, making it easier to repair. Since the sensors have already been configured using the .iodd file, the debugging and replacement of the sensors are also easier.
Data generated by computers supporting IIoT can also help diagnose issues affecting product quality. For example, data from machine sensors may indicate that one of its cylinders has not completed its stroke. Corrosion in motion may lead to a deterioration in the quality of the manufactured product over time. Understanding the deviation of part functions before it affects product quality will be a significant advantage.
Providing More Effective Information
In the coming years, as these technologies gradually begin to appear in machine control systems, they will produce better diagnostics, simplified debugging, improved safety, and more consistent asset availability. These advantages will have a significant impact on machine manufacturers and end-users in the automotive, pharmaceutical, and food and beverage industries.
Users will soon apply these technologies to solve major problems in manufacturing systems. These solutions will analyze and predict based on data collected from low-level sensors measuring machine performance, thereby automatically or systematically improving overall operations. Analyzing these new data will create relevant information, enabling machines to operate more effectively with less downtime.
Leave a Comment