In 1959, American physicist Richard Feynman (Richard Feynman), in his famous lecture "There's Plenty of Room at the Bottom," proposed the idea of miniaturizing machines to the scale of atoms and molecules. However, it was not until the 1980s and 1990s that MEMS technology began to be developed and commercialized.
In 1962, the pioneer of micro devices—the first silicon micro pressure sensor came into being, marking the beginning of MEMS technology and also the starting point of MEMS micro sensors. Relevant papers from Honeywell Research Center and Bell Labs show that they invented the first silicon diaphragm pressure sensor and strain gauge.
Since then, people's interest in MEMS sensor technology has grown rapidly. By the late 1960s, many pioneering American companies had already begun to produce the first batch of MEMS pressure sensors.
The development of MEMS technology has been rapid and plays a key role in the popularization of today's sensors. Without MEMS technology, the miniaturization, integration, and low power consumption of sensors would be difficult to achieve, and the development of the Internet of Things, smartphones, automobiles, and other fields would be severely lagging behind.
Advertisement
Nowadays, a variety of MEMS sensors and actuators have achieved commercial success, replacing traditional devices and being widely applied. The global shipment volume is in the tens of billions per year. In this article, let's take a look at these MEMS sensors and actuators that have achieved great success.
MEMS Microphone: Popular on mobile devices as soon as it was launched.
In 1961, the famous Bell Labs developed the first electret condenser microphone (ECM), which uses the change in the size of the capacitance on the diaphragm caused by the sound to convert sound into an electrical signal.
After that, the electret condenser microphone became popular nationwide for more than 40 years, until 2003, when the first commercial MEMS microphone product appeared on the market—the SiSonic microphone from Knowles (Knowles Electronics).
At this time, mobile phones gradually became popular in the market and became thinner and thinner. Traditional electret condenser microphones could not meet the requirements of mobile devices for light, thin, and small microphones. The emergence of MEMS microphones was favored by mobile phone manufacturers.In 2003, Knowles Electronics took the lead in shipping MEMS microphones to Kyocera of Japan for use in mobile phones. In the same year, Motorola used Knowles Electronics' MEMS microphones in its ultra-thin RAZR phone. To date, Knowles Electronics has sold over ten billion SiSonic microphones.
MEMS microphones have achieved great success in the market, basically replacing traditional electret microphones in the market - especially in the mobile device market - and becoming the mainstream. In each of our mobile phones, there are at least more than three MEMS microphones.
According to data from Yole Development, since 2015, the shipment of MEMS microphones has gradually exceeded that of ECM - at this time, MEMS microphones have only been commercialized for 12 years, and since then, the shipment of MEMS microphones has grown by double digits year after year.
According to Yole's data, with the first-mover advantage of MEMS microphones, Knowles Electronics has long occupied the throne of the world's first manufacturer of MEMS microphones until it was surpassed by Goer Micro in 2020. The rise of MEMS microphone manufacturers such as Goer Micro, AAC Technologies, and Minxin Shares reflects the development of China's MEMS industry.
MEMS Inertial Sensors: Making Inertial Measurement of Mobile Devices Possible
Did you know? The world's first truly large-scale commercialized MEMS sensor is the accelerometer, which was invented by the American company ADI (Analog Devices) in 1991. This sensor is based on the principle of capacitive sensing, and the output signal of the sensor can be used to measure acceleration or tilt.
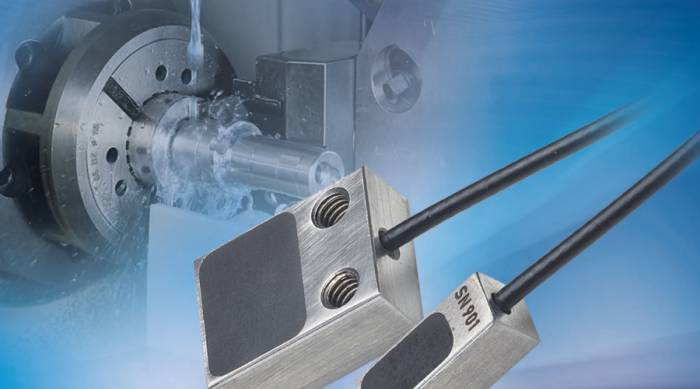
This MEMS accelerometer is mainly used in automotive airbags. Before that, traditional sensors for automotive airbags were priced at $20 each, while ADI's MEMS accelerometer sensor was priced at about $5 each, which reduced the cost of electronic devices for airbags by about 75%.Subsequently, MEMS inertial sensors rapidly gained popularity, replacing traditional inertial sensors in many fields such as automobiles, and creating more application scenarios—such as the possibility of inertial measurement in mobile devices like smartphones, smartwatches, and TWS earphones.
MEMS inertial sensors mainly include MEMS gyroscopes, MEMS accelerometers, and MEMS-IMUs (Inertial Measurement Units).
In smartphones, MEMS accelerometers are responsible for sensing motion status, and by measuring the acceleration of an object in three directions, they achieve various functions such as automatic screen rotation, pedometers, and game controls.
Currently, the most successful suppliers of MEMS accelerometers in the market are Bosch, STMicroelectronics, Murata Manufacturing, NXP Semiconductors, and Analog Devices, with Bosch and STMicroelectronics leading in market share at 32% and 21%, respectively.
Gyroscopes sense the rotation state of an object by measuring angular velocity. Since Sperry invented the world's first practical gyroscope, gyroscopic technology has undergone nearly a century of development and is the core of inertial technology.
In 1989, the first micro-mechanical gyroscope using MEMS technology was introduced, with a drift rate of 10 degrees per hour. Compared to other gyroscopes, MEMS gyroscopes have lower costs, smaller sizes, higher reliability, and are easier to mass-produce, making it possible to use gyroscopes in mobile devices.
The iPhone 4 was the world's first smartphone with a built-in MEMS three-axis gyroscope, capable of sensing motion, acceleration, and angle changes from six directions.
In smartphones, the gyroscope works in conjunction with GPS, geomagnetic sensors, etc., to achieve precise positioning and navigation functions. At the same time, the gravity sensing characteristics in the game are more powerful and intuitive, greatly enhancing the gaming experience. This feature allows the phone to continue navigating for users based on the acceleration direction and magnitude sensed by the gyroscope when entering a tunnel and losing the GPS signal. The three-axis gyroscope will combine with the iPhone's existing proximity sensor, light sensor, and direction sensor to bring the human-computer interaction capabilities of the iPhone 4 to a new level.Nowadays, with the rise of drones and autonomous driving technology, the application of MEMS gyroscopes is becoming more and more extensive, providing stable and reliable attitude control for these devices.
The main manufacturers of MEMS gyroscopes include TDK, Analog Devices, Honeywell, Bosch, STMicroelectronics, and others.
MEMS-IMU (Inertial Measurement Unit) is composed of MEMS accelerometers and MEMS gyroscopes, with the capability to measure acceleration and angular velocity, and has a very wide range of applications. The first micro-electromechanical inertial measurement assembly was developed by the American Draper Laboratory in 1994.
The development of MEMS IMU was initially driven by military needs, and then gradually extended to civilian use, and has now been widely applied in fields such as consumer electronics, automotive, and industrial automation.
At present, with the rapid development and cost reduction of MEMS IMU technology, there is a trend for MEMS IMU to gradually replace independent MEMS accelerometers and MEMS gyroscopes.
MEMS pressure sensors: driving the extension of pressure detection to miniaturization
Pressure is the second largest measured physical quantity. As mentioned earlier, the world's first MEMS sensor was a silicon micro pressure sensor, which was developed by Honeywell in 1962.
At present, Honeywell's pressure sensor products cover a variety of scenarios. Their absolute pressure, gauge pressure, true gauge pressure, and miniaturized pressure sensors can meet the most stringent test and measurement specifications in the world's most severe environments, including general industrial process requirements and pressure sensors specifically designed for hazardous areas.Compared to traditional pressure sensors, MEMS pressure sensors have the advantages of no mechanical fatigue or aging, stable output signals, high sensitivity, small size, and suitability for mass production in large quantities (cost advantage). With the development of mobile devices, automobiles, and other areas, MEMS pressure sensors are becoming increasingly popular.
In the field of medical and health care, pressure sensors are widely used in devices such as sphygmomanometers, ventilators, and monitors, providing doctors with accurate physiological parameter data. In addition, with the rise of wearable devices, pressure sensors are also used in smart bracelets, smartwatches, and other devices to achieve functions such as heart rate monitoring and sleep analysis.
A significant advantage of MEMS pressure sensors is that their size can be made very small, which has promoted the application of pressure sensors in innovative fields such as miniaturized mobile devices and medical equipment.
For example, previously, Tyco Electronics launched the industry's first miniature invasive MEMS pressure sensor, as thin as a hair strand, which has promoted the application of pressure sensing in the field of medical equipment. In the future, this IntraSense series of sensors can be applied to minimally invasive medical devices such as diagnostic catheters, therapeutic catheters, disposable endoscopes, biopsy needles, and ablation devices. Doctors performing related minimally invasive surgeries will no longer need to rely solely on experience for operation; they can make judgments based on accurate pressure values. This will bring about a significant transformation in the digitalization of the existing medical industry.
MEMS DLP chips: Pinnacle of traditional projection equipment, pioneering the era of digital laser projection
DLP projection technology is a revolutionary development in the field of display, just as the CD had a profound impact in the audio field, DLP has turned a new page for video projection display.
The inventor of the Digital Micromirror Device (DMD, also known as the DLP chip) - Dr. Larry J. Hornbeck of Texas Instruments, was awarded the 2014 Scientific and Technical Award by the Academy of Motion Picture Arts and Sciences (i.e., the Oscar) for his outstanding contribution to the transformation of the century-old film industry into digital film technology! This fully demonstrates the significant influence of MEMS DLP chip technology on the image industry.DLP (Digital Light Processing) chips' core component is the DMD (Digital Micromirror Device), which is an important category of optical MEMS.
In 1977, the development of DLP chips officially started at Texas Instruments' Central Research Laboratory. At that time, Hornbeck first used "deformable mirrors" to control light through analog technology, but the analog technology applied was always difficult to meet the expected requirements. It was not until 1987 that he made a technological breakthrough and invented the DMD (i.e., DLP chip) based on MEMS technology, which changed this situation.
Since then, DLP technology projectors have long occupied more than 60% of the market share and have been the mainstream projection technology solution, a situation that has only changed in the past two years.
The DLP chip uses MEMS technology to mass-produce tens of thousands of "mirrors" - micro-mirrors in a silicon substrate. The following figure is a schematic diagram of the DMD chip's packaging structure, which can be clicked to enlarge for viewing.
In a DLP chip, there are millions of micro-mirrors, each of which can independently reverse motion, flip in positive and negative directions, and flip tens of thousands of times per second. The following figure shows the process of each micro-mirror on the DMD chip flipping and refracting light. Each micro-mirror can be controlled individually, refracting corresponding light to form different colors and brightness, and each micro-mirror is like each pixel point on our TV.
At present, DLP chip technology is mostly exclusively patented by Texas Instruments. According to Yole's data, Texas Instruments occupies nearly 80% of the global optical MEMS market share with revenue from DLP chips.MEMS Inkjet Printheads: Dominating the Printing World and Printing DNA Structures
In inkjet printers, MEMS (Micro-Electro-Mechanical Systems) inkjet printheads are the most crucial components, responsible for ejecting ink. Some printheads use piezoelectric thin films to vibrate and squeeze the ink, while others rely on heating to create bubbles that expand and push the ink out of the chamber.
Interestingly, these two types of MEMS inkjet technologies have formed two major camps in the printer industry. Epson and Brother represent the piezoelectric printing technology, while HP and Canon, which use thermal bubble jet printing technology, are their competitors.
At present, inkjet printers, along with laser printers and dot matrix printers, dominate the market and are one of the mainstream printing technology solutions.
Thanks to the shipment volume of MEMS inkjet printheads, printer manufacturers such as HP, Epson, and Canon have long been included in the global top 30 list of MEMS device shipments.
In addition to printing text and photos, in the field of medical and biological research, MEMS inkjet technology is also used for the construction of DNA arrays, replacing traditional ink with synthetic reagents.In the field of DNA synthesis technology, inkjet printing synthesis technology has become the most focused area due to its high throughput, high efficiency, and low cost, and has greatly promoted the development of DNA synthesis. In recent years, the number of related patents has also increased significantly.
Conclusion
MEMS technology is one of the most revolutionary high-tech technologies of the 21st century. From this article, we can see the disruptive applications of MEMS microphones, inertial sensors, pressure sensors, DLP chips, inkjet heads, and other MEMS devices in various fields. The emergence of MEMS devices has greatly promoted and expanded the application boundaries of traditional devices.
In addition to the MEMS sensors and actuators mentioned in the article, MEMS filters, MEMS thermopiles, and others are also widely used. At the same time, new MEMS technologies, such as MEMS speakers and MEMS clocks, are also showing a vigorous development momentum and are expected to disrupt the related fields in the future.
Leave a Comment