Recently, Central Control Technology released its first Universal Control System (UCS) product, Nyx. What kind of product is this? Will it replace the traditional DCS and become the future trend?
DCS, or Distributed Control System, has a history of nearly 50 years since its inception in 1975. It has become an indispensable automated control system for optimizing precise process control, improving production safety levels, and achieving digital and intelligent upgrades in the process industry.
Looking back at the Chinese DCS market in the early 1990s, foreign brands held an absolute dominant position. It was not until the end of 1993 that the introduction and successful deployment of Central Control JX-100 DCS opened up a "new map" of domestic DCS system knowledge that was independently controllable. This not only reduced product prices and introduction costs but also promoted the positive development of domestic industrial control brands.
Over the years, although minor improvements to DCS products have never stopped, due to the particularity of the application industry, many manufacturers dare not and are unwilling to make major changes. It cannot be denied that whether it is being cautious in the face of risks or being content with the status quo, it has led to the principles, architecture, design concepts, and control methods of DCS, which have never undergone major subversion and change.
Nowadays, the rapid rise of new generation information technologies such as big data, cloud computing, the Internet of Things, and AI is accelerating changes and reshaping various fields of economic society. At the same time, it also brings challenges to the integration and application of technology for automated control systems. More importantly, DCS has finally ushered in the opportunity to achieve "qualitative change" and open a new chapter in the process control of the process industry.
Advertisement
Recently, Central Control Technology, a leading domestic intelligent manufacturing company dedicated to becoming a global leader in industrial AI, released the first product of the Universal Control System (UCS) that has shaken the global automation field - Nyx. This move can be called the first subversive innovation of DCS in nearly 50 years.
It also raises people's thinking: will the emergence of Central Control UCS replace DCS and become the "new favorite" in the future?!01 Standing in the Era of Digital Intelligence: DCS is Good, but Not Good Enough
The new era of digitalization and intelligence has arrived. In the industrial field, intelligent manufacturing centered on data is the general trend of industry development. The control system, as the core of the intelligent manufacturing architecture and the foundation layer of the automatic control layer, is the core link of the "hard capability" in the intelligent manufacturing structure. It needs to have stronger data acquisition, storage, calculation, and analysis capabilities to better support the application of intelligent software at the upper level.
At present, with the continuous development of complex process industries, industrial process control has put forward new and higher requirements for the collection, transmission, and data conversion of a large number of field signals, as well as for accuracy, reliability, integrated management, and intelligence. The traditional DCS system is difficult to meet these needs, mainly for two reasons:
● Insufficient openness: Each manufacturer tightly binds their own proprietary hardware and software systems. Once a manufacturer's DCS is chosen, it is necessary to "go all the way to the end" with them. The maintenance, upgrade, and lifecycle management of proprietary hardware are very difficult;
● Poor interoperability: Although the field bus of DCS has international standards, there are many types of standards, and there are 8 types stipulated by the international standard IEC61158, which leads to poor interoperability and "data islands" are difficult to avoid.
In addition, from the perspective of user use, in addition to the limited computing power, the transmission bandwidth, speed, and accuracy of DCS, whether it is analog signal transmission or field bus transmission, cannot meet the requirements of the digital intelligence era. Moreover, the extensive use of analog instruments and field bus instruments requires a large number of I/O cards, gateways, wiring, and communication cables on the site, leading to problems such as long DCS engineering cycles, high installation costs, and difficult maintenance.
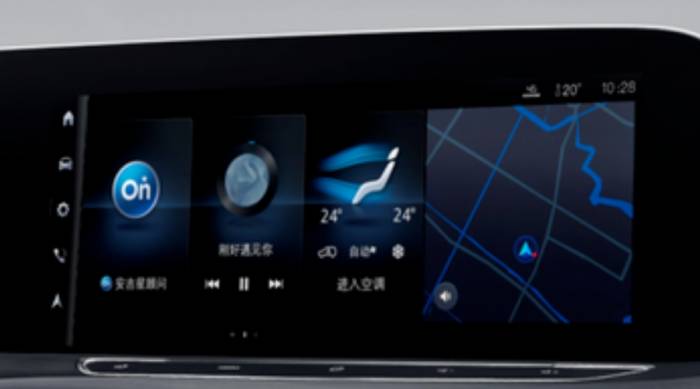
02 Starting from Architectural Design, Returning to the Essence of the Control System
The limitations of history have led to the traditional DCS not being able to meet the needs of the new era well. In the early days, the fieldbus control system (FCS), which was once seen as inevitably replacing DCS, was not widely accepted and adopted by users, and the fieldbus only existed as a bus network of DCS. Today, the process industry market is looking forward to a more advanced, more universal, and intelligent new generation of process control systems, integrating the latest technologies to help the industry move towards digitalization and intelligence.
Fortunately, the progress of new technologies has paved the way for the design of control systems to return to the essence (i.e., perception, connection, and calculation). The UCS released by Zhongkong Technology this time is based on this concept, adopting a "cloud-network-end" minimalist architecture, that is, control data centers, all-optical industrial networks, and field intelligent devices:
● The control data center is equivalent to the brain of UCS, responsible for tasks such as program execution, data processing and analysis, and control management of UCS. The difference is that it does not need to use dedicated controller hardware, but instead uses general IT infrastructure and mature cloud technology for deployment (* considering data security, real-time, and reliability, the control data center is not deployed in the cloud, but in the form of a private cloud stored locally). Software-defined means that resources can be automatically adjusted according to demand to achieve elastic and scalable computing power supply. The control data center is also equipped with NyxOS, a cloud real-time operating system designed specifically for industrial real-time control, which can provide a safe and reliable real-time control task running environment. In addition, redundant and distributed deployment architecture can also ensure the high availability and fault tolerance of the control system.● The all-optical industrial network refers to the use of fiber optic connections for all links between the control center and field devices, with field data reaching the control center at a speed of 10Gbps and in a parallel redundant manner, saving more than 80% of cables and space.
● Field intelligent devices are the sensor, actuator, and field instrument parts of UCS. In UCS, the central control adopts field connection technology based on Ethernet-APL (Ethernet Advanced Physical Layer), supporting zone 2 intrinsically safe explosion-proof field connection boxes and APL modules, achieving instrument IP-ization and increasing communication speed by more than 100 times.
It can be seen that compared with the traditional DCS architecture, UCS, which only has "cloud-network-end" three levels, has indeed opened up a new situation in the development of DCS control systems and has extraordinary significance across the times.
03 Open software definition, the "prime time" for UCS has really arrived
Looking back at the past, under the pressure of foreign-funded enterprises with absolute market discourse power, local industrial control enterprises often hesitated to choose "persisting in independent innovation" when facing the choice between "surviving by acting as an agent for foreign brands". Now, with decades of accumulation and development, the central control has broken through in the industrial automation market full of experts with the concept and products of UCS, which is undoubtedly a milestone that makes the Chinese proud.
The innovation of the UCS concept is naturally important, but for the process industry with high requirements for "safe, stable, long, full, and excellent", if it cannot create benefits for corporate production, everything is empty talk. And software definition, full digitalization, and cloud-native are not only the current development trends of control technology but also three typical characteristics of UCS. It is reported that these characteristics also allow UCS to greatly reduce corporate costs, reduce the space of the cabinet room by 90%, reduce the cable cost by 80%, and shorten the construction period by 50%.
For example, on the one hand, the minimalist UCS architecture has brought unprecedented changes to the control system. It has broken the shackles of traditional physical controllers, I/O modules, and cabinet groups, and broken through the constraints of traditional DCS closed proprietary, hierarchical rigidity, and limited computing power, making the control system do not need a large number of control cabinets, which is self-evident to the users.
In terms of development, just as the "U" (Universal) "universal, open" in UCS, UCS has fundamentally achieved the decoupling of software and hardware. The software system does not need to be developed specifically according to the hardware, only the programming language commonly used by IT personnel is needed. In this way, it reduces the difficulty of development and maintenance, and also conforms to the development trend of IT/OT technology accelerating integration.In the field of technological integration and application, due to the fact that the control data center of UCS is deployed on a private cloud, it has an inherent advantage in introducing the latest IT technologies. Ecosystem partners can fully develop cloud-native apps based on a universal platform to achieve rich functions, which would be very difficult for traditional DCS to integrate these technologies at the control level.
In the era of digital intelligence, APL, with its unique advantages, has become the best choice for field instruments and actuators with large amounts of data, and the central control has long been aware of this development trend. Field devices based on APL bring a fully digital signal transmission mode to UCS. APL based on Ethernet can not only achieve high bandwidth of 10Mbps and long-distance communication of 1000 meters, but also realize data transmission and power supply for field devices, meeting the explosion-proof design specifications. In addition, APL instruments can also completely replace 4-20mA+HART instruments, eliminating the I/O cards originally responsible for analog-to-digital conversion.
In addition to forward-looking insights, to achieve easy integration of APL devices, the central control has made full preparations and started researching APL technology as early as 2019. At present, based on years of technical and know-how accumulation, the central control has a full range of APL products such as power switches, field switches, and field instruments, and actively builds an industrialized ecosystem, cooperating with more than 20 domestic and foreign instrument manufacturers. The types of instruments cover all mainstream process measurement instruments, as well as the vast majority of optimization and analysis instruments.
Of course, UCS also supports existing 4-20mA+HART instruments. Just add an APL converter to these instruments, and they can be connected to the system. It can be seen that at every stage before, during, and after the birth of UCS, the central control is no longer the difficult "feeling the stone to cross the river" in the early years, but has a well-thought-out plan for every detail.
04 Integration of industrial AI, "changing the track to overtake" to release more value
In today's booming IT technology, it is very important for domestic industrial automation manufacturers to keep pace with the times and find breakthroughs to achieve overtaking in the curve or change the track. Nowadays, AI technology has entered the industrial field for some time, greatly changing the development and competitive landscape of various industries. For UCS, integrating AI technology is not difficult. In Nyx, the central control proposed the AI-Inside design concept, that is, AI empowers control.
At present, Nyx has achieved AI-PID, a control loop optimization function based on reinforcement learning, and AI-assisted programming that can assist in generating control algorithms through natural language or design documents. These two functions have shown amazing control effects and engineering efficiency improvements, and the potential of AI in predictive maintenance, alarm prediction, digital twins, and other aspects in the future is also worth looking forward to.
For users, safety and reliability are the two most criticized points of the system's open architecture. When designing UCS, the central control considered these issues. First, the hardware of the control data center has been designed for reliability, including redundant design of key components, and the use of highly reliable hyper-converged technology. Moreover, 99% of the hardware and software of the data center have fault risk diagnosis and analysis, which can identify risks in advance.In terms of information security, UCS has moved away from the traditional strategy of layered defense and has adopted a more advanced Zero Trust security framework. All data access must go through authentication, authorization, and continuous verification. Previously, OT technology was usually lagging behind IT, making it difficult to implement Zero Trust security. However, with UCS adopting common IT infrastructure, the popular Zero Trust technology in the IT field can naturally be applied.
Starting from Industry 3.0, now Central Control relies on its strong R&D and supply chain partner strength, and continues to focus on Industry 4.0. This also gives UCS a powerful universal and open characteristics, making it easy to control and integrate advanced IT technologies such as AI and Zero Trust, allowing it to release unlimited industrial application value in the future "Artificial Intelligence" era, thus becoming a disruptor and substitute for DCS.
On the other hand, the deep integration of industrial AI technology is also expected to become the "killer weapon" for Central Control to pull away from domestic and foreign peers. Just like the "changing lanes overtaking" in the new energy automobile field, whether UCS can replace DCS to achieve "changing lanes overtaking" in the industrial control field is also worth looking forward to.
05 From running in parallel to leading, and looking at the new future of the rise of domestic products
In recent years, in order to solve the problem of domestic autonomy and controllability, a number of local DCS companies have been supported to compete with foreign brands. After decades of rapid development, now, China's DCS market has entered a relatively stable and mature period. In fact, before the launch of UCS this time, the main product of Central Control Technology's DCS was the large-scale joint control system ECS-700, which was also the first excellent product to break the monopoly of foreign companies on the core control system of China's petrochemical industry.
With the continuous penetration of the Internet into the field of industrial control, users' usage habits, needs, and expectations have undergone tremendous changes, and the concept of "software-defined control systems" has also had more fertile soil. Central Control Technology, from proposing the UCS architecture to successfully creating the first UCS product Nyx, is thanks to its world-class engineering and R&D capabilities, as well as a capable professional team.
Now, Central Control is conducting a comprehensive exploration in the field of industrial AI, aiming to accelerate the iteration and reconstruction of product technology with AI, and promote a revolutionary transformation of the process industry. UCS is one of the outstanding results.
Looking around the world, at present, we are at a critical moment of a major change that has not been seen in a hundred years. Looking at the field of industrial automation control, the previous century, we have been following the development of the world. And this time, with the increasing maturity of IT technologies such as cloud technology, AI, and software-defined, and the emergence of new generation technologies in industrial communication and intelligent instruments, Central Control, based on more than 30 years of technical and industry knowledge and experience in the field of process control, has launched the pioneering UCS, which may lead more national industrial control brands to rise in the new century and lead the development of the global industrial control field!
Leave a Comment