Although PID control is a good choice for most process control applications, sometimes the challenges of the application are too great or too complex. In such cases, there are six strategies that can simplify the process.
The Proportional-Integral-Derivative (PID) control scheme is a common method used by Programmable Logic Controllers (PLCs) and Distributed Control Systems (DCS) to control complex processes and manage dynamic industrial systems. Many available online resources focus on the basic principles of setting and control loop tuning methods for controlling deviations and minimizing process fluctuations, including how to select initial gain, when to use derivative control, and how to adjust PID to obtain response time and reduce overshoot.
Although PID control is a good choice for most industrial control applications, sometimes it is not enough to handle systems that are challenging or cannot be reduced to simple set points (SP), process variables (PV), and control variables (CV). Some systems have a long dead time, which is the time required from the change in CV to the significant change in PV. In such cases, there are six advanced strategies that can simplify the process and help supplement PID control in challenging applications.
Advertisement
01 Tune the instrument for better PID results
The PV input of the PID drives the operation of the rest of the control loop. Noisy measurements can make the deviation calculation (the difference between SP and PV) unstable.
If the deviation shows significant changes or fluctuations within a single cycle of scanning the input and output (I/O), then the derivative output will be large, and the CV will immediately rush to the minimum or maximum value. Adjusting or replacing the instrument that produces the noisy PV can transform an unstable control loop into a well-performing system.
02 Signal filtering to clean up PID information
Some process parameters are noisy, and the instruments accurately record these noises. One way to deal with this noise is to use signal filtering. This method includes using a time-based filter for the PV and replacing the instantaneous signal with the average value over a certain period.
When selecting a filtering scheme, the goal should be to eliminate noise while preserving as much meaningful signal as possible. It is important to remember that the PID integral term is a time-filtered evaluation of the deviation, so filtering is applied twice. To control a noisy PV, some control loops are adjusted too aggressively. In this case, reducing the gain to detune the PID will be more effective than signal filtering. Signal filtering may hide important process information from operators and control loops, so it should be used with caution.03 Cascade Control, using one PID to control another PID
Another method for controlling high-difficulty PVs is to use one PID to control another PID, which is known as cascade PID control. The high-priority PV is fed into the low-speed master PID, which sends the dynamic SP to the fast secondary PID, and this secondary PID controls a different secondary PV, which then affects the master PV through process interaction. For example, the pressure of a steam heat exchanger is a rapidly changing attribute that can be controlled by adjusting the slow temperature of the fluid flowing out of the heat exchanger. By controlling the secondary PV (pressure), the primary PV (temperature) can be made to reach its SP value more quickly and maintain it on the SP value, almost without the oscillation that occurs when using a single PID to control temperature directly.
04 Feedforward Control: Based on Anticipated Future Changes
Sometimes, control system designers know exactly how the PV will react when the CV changes, and they can encode this knowledge into the control strategy. This is the widely used feedforward. The PID system is essentially a feedback scheme, where the CV changes, and the resulting PV changes are measured to calculate a new deviation item. In feedforward, the control logic uses the CV change to calculate the expected change in the error item and uses it for PID logic.
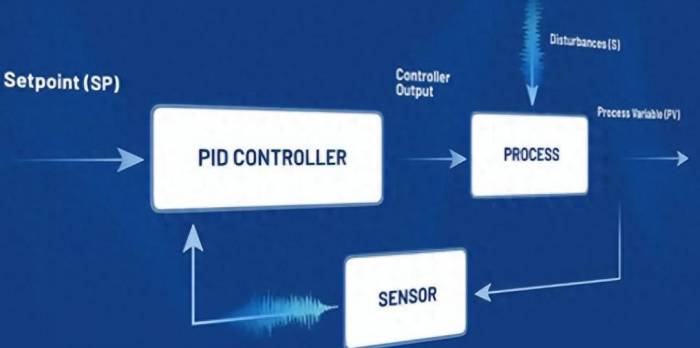
Many modern PID control logic objects include an input for a feedforward term, which usually has its own gain adjustment constant. Generally, if there is a problem with the proportional-integral (PI) controller, the best way to improve it is to add some feedforward items instead of increasing the derivative control, provided that the appropriate feedforward variables can be found.
05 Gain Scheduling Can Sometimes Help PID
For processes that are nonlinear within a predetermined operating range, if each segment of the operating range essentially has a linear response, then PID control is still an option. Proportional, integral, and derivative gains can be determined for each segment and then programmed into the PID object to change as the process moves along different linear domains. This is usually called gain scheduling.
Be cautious when performing gain scheduling, and pay special attention to the boundaries of the gain ranges. If the process often operates near the boundaries, consider changing the gain scheduling to avoid frequent switching between gains.
06 Model Predictive Control Can Utilize the Power of the Controller
Modern PLCs and DCSs use faster central processing units (CPUs). Some people may remember that great care was taken to manage the controller's memory usage and clock cycles to avoid controller failures or skipped routines. Now, the CPU of the controller has amazing computing power, which has opened up innovations in control schemes called model predictive control (MPC). In MPC, control system engineers work with experts in the physical process to design a mathematical model for the physical process and place it in the controller. This real-time process model allows the control logic to predict all relevant PV changes under different CV settings. These predictions are used to determine the best CV changes required to achieve the overall process state.For controlling complex processes or dynamic industrial systems, basic PID control is often sufficient, but it is by no means the only tool available. There are many different options that can be used to control these processes and systems. By combining these options in various ways, the results required by operators and production needs can be achieved. When a process seems destined to oscillate and requires continuous, active supervision by operators, the advanced control strategies introduced here can be considered. They can transform the most challenging processes into reliable, high-uptime, almost trouble-free parts of a smoothly operating facility.
Key concepts:
■ Understand the role of PID in process control.
■ Understand the six strategies that can assist PID in challenging operating conditions.
Leave a Comment